Introduction
One of the challenges in heavy machinery is optimizing machine output and reliable equipment. Working in an industry such as trucking, railroad, mining, construction and manufacturing can be high demand, so it is critical your equipment is safe and can perform at its best in harsh conditions and outdoor environments.
That’s why so many businesses trust Huck® fasteners for their feeders, trucks, truck trailers, buses, railcars, mining screens and other equipment. Backed by over a century of experience creating innovative fastener solutions, Huck® fasteners are precision engineered to provide permanent, vibration-resistant joining solutions for industrial applications.
A clean and safe alternative to welding and a more efficient fastening method compared to standard nuts and bolts, the shear strength of Huck® fasteners makes them reliable in situations where a joint is integral to the durability of your equipment’s structure.
What are the benefits of Huck® fasteners?
Huck® fasteners offer multiple benefits that other fastening methods cannot – they are the tough solution to most fastening problems.
- Quick and easy installation using simple tools can reduce production time by up to 75%. It also means you don’t need to invest in specialists for installation.
- The reliability of the fastener means that you don’t need to re-check or replace it, which reduces overall costs to your equipment.
- Each Huck® bolt and structural rivet has its own characteristics, so there are products available for each unique application and need.
- Huck® fasteners will not loosen, even under extreme vibration.
- Welding can pose a potential risk to workers due to random sparks and the safety hazard of spent rods and remnants on the assembly floor. Huck® fasteners offer a safer, cleaner alternative.
- Once the Huck® fasteners are installed, they can’t be removed without specialist tools.
- Huck’s fasteners solve the problem of any fasteners or bolts loosening over time by creating a tight fit and local system that can withstand rugged conditions.
- Minimal training is required for operators installing the fasteners, eliminating the dependency on an operator’s skillset. The need to torque or apply a specified rotation to a threaded fastener has been eliminated and, as such, lessens the degree of skill required to effect proper installation. Unskilled operators with minimal training can quickly achieve consistently high-quality structural connections from first installation.
- Quality control measures are simple to implement, as operators can easily visually inspect the fastener for the correct locking collar swaging during installation.
- You will experience less downtime caused by bolt loosening and equipment failure.
- Equipment performance is directly affected by weight – saving weight in your equipment is essential. Huck® fasteners can help lighten the load by offering a higher strength solution, meaning you can use less fasteners or a smaller diameter Huck®. They also allow for the use of lighter weight aluminum instead of steel in the joining process.
How do Huck fasteners work?
High strength fastening systems are installed with either manual, pneumatic or hydraulic installation equipment, making it user-friendly for operators. Using the most advanced fastening technology to date with a unique lock-bolt design, the strength of the fasteners comes from the shear resistance of the collar material and the number of grooves it fills.
What industries do Huck® fasteners thrive in?
Huck® fasteners thrive in structural applications where the working environment is subject to shock, vibration and dynamic loading. They are relied upon by businesses in many industrial markets including truck, trailer, stock crates, bus, rail, bridge work, automotive, HVAC, green energy (such as wind farms), agriculture, grain silo’s, mining, oil and gas.
Blind Bolt Characteristics
Most blind bolts are designed with a steel pin, a collar, and a sleeve.
There are various characteristics to consider when choosing the right blind bolt. You need to choose the right grip range length and diameter for optimal strength and lasting performance. You usually can find the right blind bolt dimensions by consulting the manufacturer’s range chart. You also have to choose the right material. Most commercial blind bolts are made of steel, but there are alternate materials, such as stainless steel and titanium blind bolts, for specialty applications such as aerospace. Once you select the right blind bolt for the job, you will have an extremely strong and lasting joint.
In addition to being strong, Huck® blind bolts are resistant to vibration. Once installed, they will not work loose over time or weaken under constant shaking. That is why they have become the fastener of choice for airplanes, railway cars, automobiles, factory equipment, mining equipment, ships—any application in which the bond has to maintain a strong connection under ongoing vibration.
Another attractive feature is that blind bolts are tamper-proof. Because they are installed using special equipment and have no screw heads, they can’t be vandalized, making them ideal for use in public transit systems, public restrooms, public buildings, or anywhere vandalism is an issue. The core bolt itself is very hard, which makes it difficult to remove without special equipment from the manufacturer. If you have the right equipment, you can remove a Huck® blind bolt and leave the parent material and the pre-drilled hole undamaged.
A Brief History of Blind Bolts
Wooden planes could no longer meet the needs of aircraft design, so engineers started to design airplanes made of aluminum, a material that was stronger, yet light enough for aircraft design. Initially, these aluminum airplanes were made using solid rivets, which made assembly slow and required two workmen, one on each side of the material being assembled. To address the problem, Jacques Chobert, one of the engineers at Aviation Developments, created a new riveting technology, the Chobert® riveting system, which could be installed from one side by one worker. Installation was still slow because fasteners had to be loaded and installed one at a time, so Aviation Developments created a tool that could hold multiple fasteners, which considerably sped up production.
Since World War II, the blind bolt has evolved to become a mainstay of manufacturing. New materials were adapted, as were new head configurations and designs. New methods were developed to machine the blind bolts so they became virtually invisible when painted. With these improvements, blind bolts became common in making aircraft ailerons and flaps, doors, floors, elevators, and so on. Pneumatic tools also were developed to speed up assembly. Over time, blind bolts were being made to join thin-gauge steel, plastics, fiberglass, and other materials. The automotive and electronics industries standardized Huck® blind fasteners for assembly uses. As new applications in aerospace and transportation emerged, new blind bolts were developed, capable of handling more extreme loads and temperatures. Uniquely designed structural rivets such as the Huck® BOM, Huck® Magnalok, and Huck® Magnabulb were developed for thin sheet materials. Eventually, blind bolts came to be used in place of rivets or bolts because of their ease of installation and superior performance.
Common Applications for Huck® BOM Blind Fasteners
Huck® BOM
The Highest Strength Blind Oversized Fastener Available
Blind bolts are used in almost every industry and application.
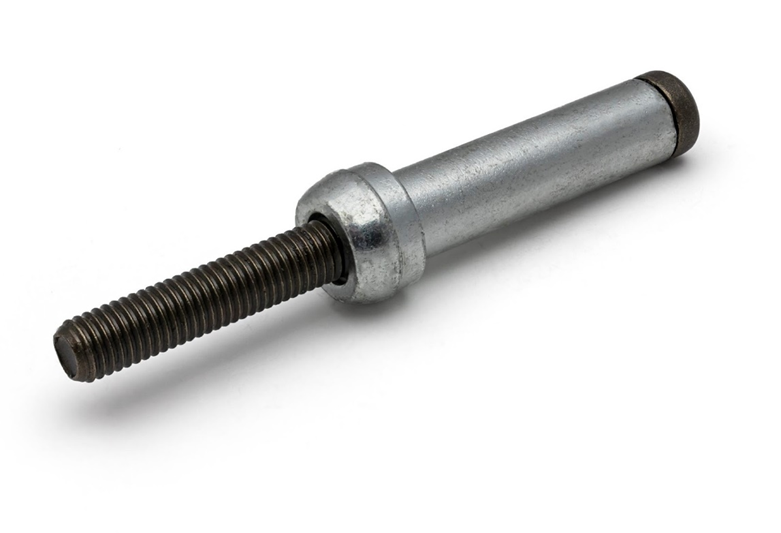
Often used as a replacement for welding, Huck® BOM is so strong, one BOM (Blind, Oversized
Mechanically locked) fastener can do the work of up to four conventional fasteners. Its unique push-
and-pull installation design makes it ideal for military vehicles, auto suspensions, rail car assembly,
and much more. BOM’s high fatigue thread form extends the life of any structure. Offering accurate,
easy, quick installation, BOM requires no special training or skills for operators.
The BOM® (Blind, Oversize Mechanically locked) fasteners from Alcoa Fastening Systems are so
strong, one can do the work of up to four ordinary fasteners.
You won’t find a more vibration resistant blind fastener, or one that works harder in so many
different applications. With its unique push-and-pull installation design, the BOM fastening system is
tough enough for military vehicles and equipment, auto suspensions, amusement park rides, rail car
assembly, and automatic storage and retrieval racks of shaft steel construction. Even the most
demanding high-tensile application is no match for the strength of the BOM fastening system.
Quick and Economical to Install and Inspect
Because installing BOM fasteners is so easy, a worker can learn the installation procedure in just 10
minutes, eliminating the need to hire certified welders or specially trained employees. And because
they install from just one side, they can be used in all blind side applications.
Installations are more accurate than other fasteners of the same kind, because the element of
human error is not an issue. In other words, correct installation doesn’t depend on operator skill or
specialized tools. Plus, chances are you can start using BOM fasteners immediately with your current
tools, saving you more money in the long run.
- Excellent pull-up and high retained clamp
- High fatigue thread form extends the life of your structure
- Often used as a replacement for welding
Materials: Steel
Available Sizes: 3/16″,1/4″,5/16″,3/8″,1/2″,5/8″,3/4″
Benefits:
Unmatched installation speed ✓
Low overall installed cost ✓
Vibration resistance ✓
Quiet non-torque tools ✓
No repetitive stress injuries ✓
Eliminates need for secondary operations ✓
No special training or skills required for operators ✓
High strength/diameter ratio:
Can be used in demanding structural applications as an alternative to threaded fasteners or welding. Very high joint tightness when compared to conventional blind fasteners. BOM is extremely difficult to remove, making it resistant to tampering.
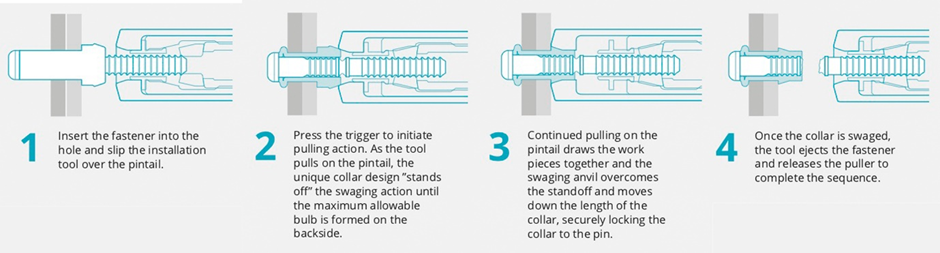
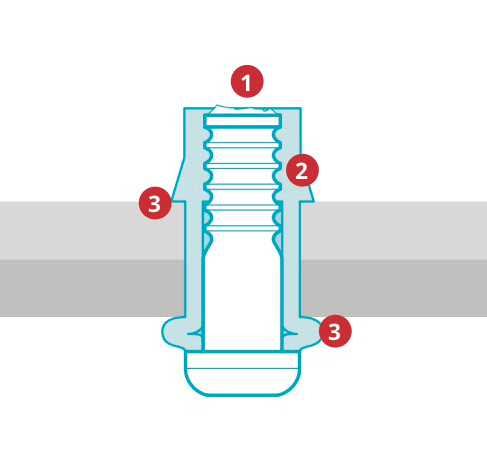
- When the pin separates near flush, the BOM fastener is installed correctly. The BOM fastener does not require surface preparation, grinding or filling after installation.
- The collar is locked to the pin through the “swaging” process, creating a high vibration resistant connection and the highest strength of any blind fastener.
- Large bearing area on both sides of the work piece ensures a permanently held, tamper resistant joint.
Installation Tooling
Installation Tools
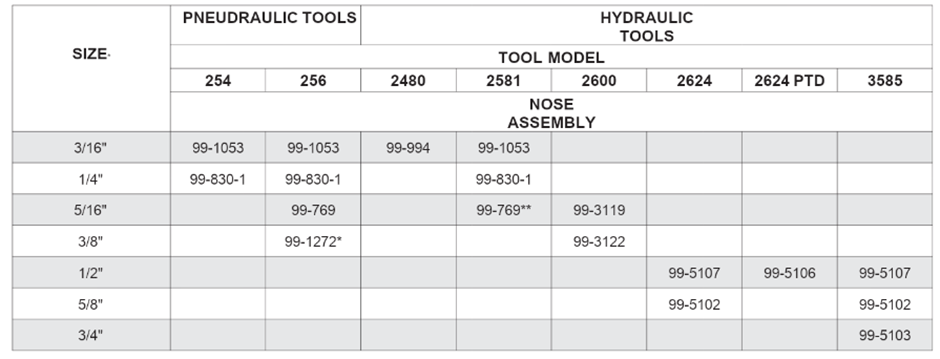
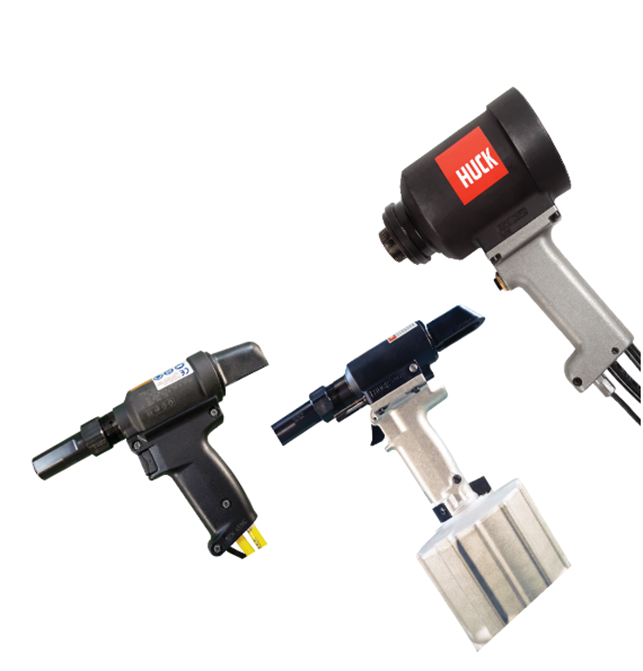
Tooling Weight and Dimensions
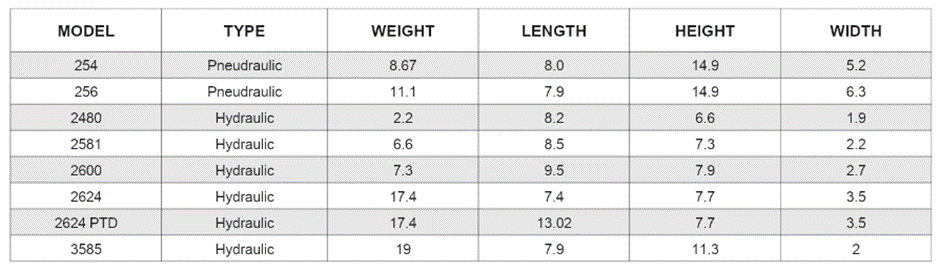
CONCLUSION:
Huck® BOM are used in the fabrication of military equipment, auto suspensions, truck, amusement park rides, and other applications that require a strong, lasting join and vibration resistance fastener is a priority to the application. It’s clear that Huck® plays an important part of the fastener world. They are relied upon by businesses in many industrial markets
Macros Fastening Systems brings quality parts to hard-working businesses and has offered high-quality Huck fasteners for many years. Contact us today on +91 9831045458 to get your queries resolved.